開発が進む水素関連技術の動向(水素貯蔵編)
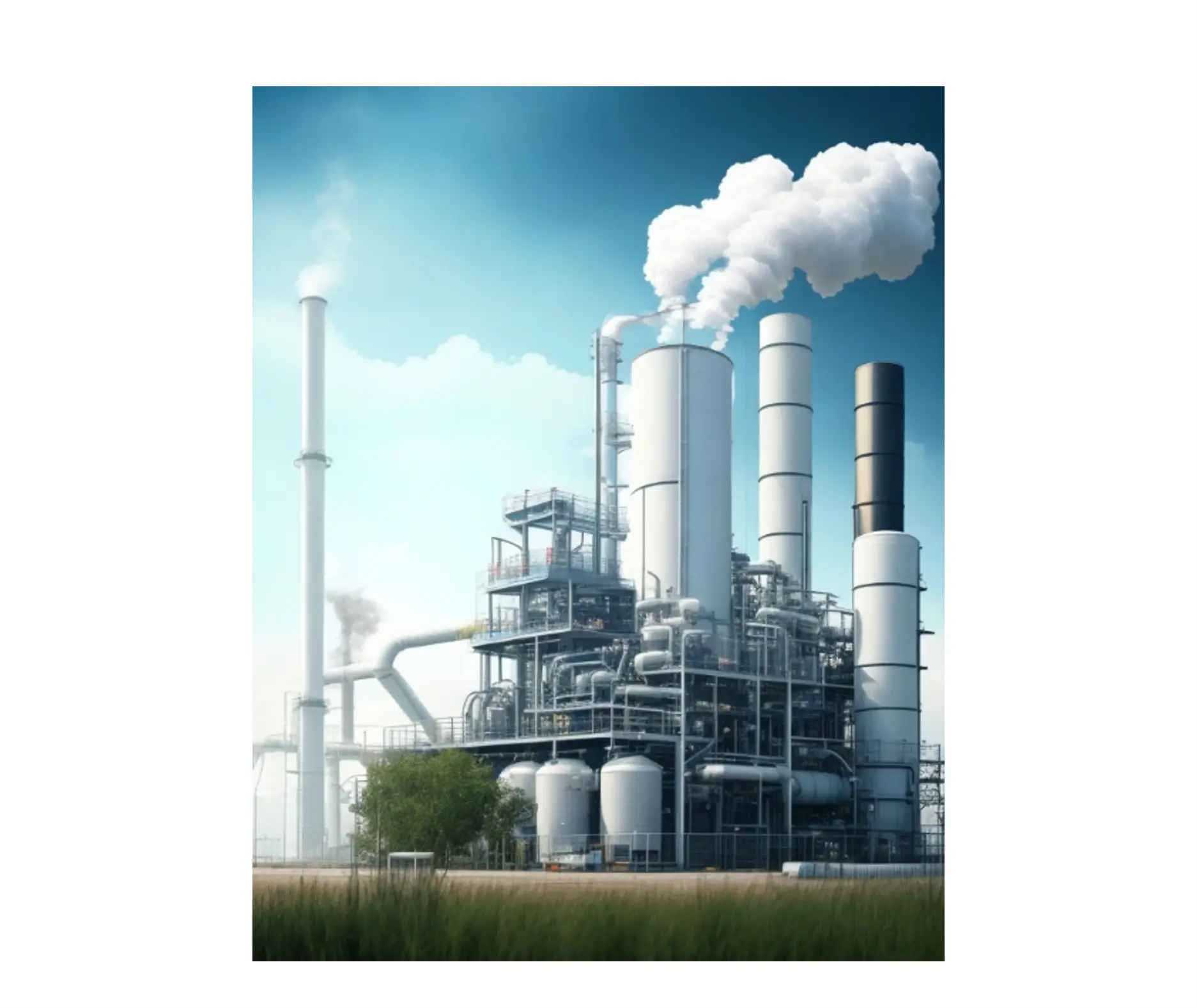
再生可能エネルギーと組み合わせた水素利用に注目が集まるが、水素は貯蔵・運搬において様々な課題を抱えている。本稿では、水素の貯蔵方法に焦点を当て、課題解決に取り組む企業や研究機関を紹介する。
水素貯蔵の必要性と現状
カーボンニュートラル実現のために様々な分野で化石燃料の置き換えが進められている。多くの場合、化石燃料の置き換え候補となるのはEVなどの「電化」技術だが、分野によっては電化だけでCO2排出ネットゼロを実現することが難しい。
例としてよく上がるのが、鉄鋼業だ。
鉄鋼生産では鉄鉱石を還元して鉄にするために鉄鉱石とコークス(石炭を蒸し焼きにしたもの)を混ぜて炉の中で熱する。
鉄鉱石は酸素を失って還元されるが、コークスは酸化されてCO2となり排出されるため、この方法ではCO2排出ネットゼロを実現することができない。そこで注目を集めているのが水素を用いた還元製鉄技術だ。
コークスの代わりに水素を用いれば排出されるのは実質水のみとなる。
他にも、トラックや船舶などの長大なモビリティーでは電池の重量増加に伴ってエネルギー効率が落ちるため、将来的にはEVよりも水素燃料の方が有利と言われている。こうした背景のもと、水素関連技術の開発に世界中から資金が投じられてきた。
商業的な水素関連事業は、製造・貯蔵・運搬・利用の4段階に分けられる。水素製造については近年急速に技術革新が進み、2020年以降の投資額の増加も著しい※1。こちらに関しては下記の記事で取り扱ったので、併せてご覧頂きたい。
参考記事:急速に資金調達が進む水素関連スタートアップ(電解槽編)
水素製造技術への投資が盛り上がりを見せる一方で、水素貯蔵技術は未だ発展途上だ。
水素を今よりも気軽に利用するためには貯蔵段階のコスト、利便性、安全性などの課題について解決が待たれる。
様々な形で模索される水素貯蔵
水素は常温で気体であり、液体のガソリンと比べて体積当たりのエネルギー密度が低い。気体のまま保存しようとすると、大きな空間を占有することとなる。
常温常圧で水素を貯蔵する三菱重工のプロジェクト
常温常圧で水素を貯蔵するにあたっては、地下の巨大な岩塩空洞を利用する方法が検討されてきた。こちらは三菱重工が米国ユタ州に建設する水素製造・貯蔵ハブが有名だ※2。
三菱重工グループはこのプロジェクトのために特別目的会社を設立し、米国エネルギー省から544m$の融資保証を受けた。
ただし、岩塩空洞をはじめとしたガスバリア性の高い地下空洞は現有する地域が限定的であり、動かすこともできない。一時的な保存のためには有用だが、他の用途に利用するためには別の形で貯蔵し、運搬する必要がある。効率的に運搬・利用するならば、パイプラインを建設する、または、水素を圧縮する技術が不可欠だ。
パイプラインでの輸送・供給
水素は天然ガスと同様、パイプラインを通じて供給することができ、石油メジャーのExxonMobil(米)、TotalEnergies(仏)と日本の鉄鋼メーカーJFEスチールなどが共同で研究開発を行っている※3。
パイプライン建設に関しては大量の資本や政治的合意形成の他、安全性も課題だ。水素は鋼材を腐食し脆くする性質を持ち、一度漏れだせば火気がなくとも爆発する危険がある。
圧縮して運搬する場合、その方法は大きく分けて4つある。高圧貯蔵・液化・吸蔵・化学変化だ。それぞれの方法はメリット・デメリットを有し、利用目的に応じて使い分けられる。以下では、各方法について詳細を掘り下げつつ、関連する企業や現在の開発状況を紹介する。
高圧貯蔵によるアプローチ
気体を高圧にして圧縮・貯蔵する方法は、プロパンガスなどの可燃性ガスの貯蔵・運搬にも用いられてきた。
水素においてもこの方法は有効であるが、水素が金属中に入り込み脆くする性質から、プロパンガスボンベと同じ素材のボンベで水素を貯蔵することはできない。水素を高圧で貯蔵するためには水素によって脆くならない特殊な合金や複合樹脂材料などが必要だ。
高圧貯蔵は水素の貯蔵方法として最も一般的な方法で、水素燃料電池車などのタンクにおいても圧縮した水素が貯蔵されている。圧縮水素タンクの開発に携わる企業も自動車と関連する業界に多い。
水素燃料タンクを開発するNPROXX
オランダのスタートアップNPROXX※4は高積載のトラックやバス、船舶用の水素燃料タンクを開発している。
NPROXXの強みは炭素繊維強化樹脂を用いることによる高耐久・長寿命の実現だ。最大700bar※5の圧力で水素を貯蔵でき、交換することなく30年間の使用を保証している。
また、NPROXXは、電解槽技術を保有するCummins(米)と2020年に合弁会社を設立した※6。この合弁会社は鉄道用途の水素貯蔵タンク開発を進めている。
トヨタも水素燃料電池で高圧貯蔵を活用
日本の自動車メーカーであるトヨタも水素燃料電池自動車用のタンクを開発している※7。既に販売されている水素燃料電池自動車MIRAIでは700barの圧力をかけ、体積にして1/450にして水素を貯蔵できる。
水素を車載燃料として利用する際に問題となるのは水素の体積エネルギー密度だ。ガソリンが約9,600Wh/Lの体積エネルギー密度を有するのに対し、700barにおける圧縮水素の体積エネルギー密度は1,290Wh/Lと、約1/8しかない※8。これは水素元来の性質であり、仮に液体水素を用いたとしても体積エネルギー密度は2,330Wh/Lと、ガソリンには遠く及ばず、改善の余地があまりないデメリットだ。
一方で、質量エネルギー密度で比較すると、ガソリンが約12,800Wh/kgであるのに対し、700barの圧縮水素は39,400Wh/kgと、3倍以上のエネルギー密度となる。ここは明確なメリットだ。
液化貯蔵によるアプローチ
水素は-253℃(20K)まで冷却すると液体となり、気体状態と比較した体積は約1/800になる。
天燃ガスも冷却・液化させてタンカーで運搬されているが、水素でも同様の運搬が可能だ。こちらの方法は圧縮水素と比べ、大量の水素を一度に運搬できるというメリットがある。
ただし、天然ガスの沸点が-162℃程度であることと比較すると、水素の沸点は極めて低い。液化させる段階でも、液体状態を維持するためにも大きなエネルギーが必要だ。具体的には、現在の水素液化システムでは投入した電力の75%以上が液化のために消費されてしまう※9。
結果として、水素を液化させ、貯蔵・運搬すると莫大なコストの発生が避けられない。現状での液体水素利用は、極低温までの冷却が必要な場合や、ロケットエンジンなどコスト度外視で高い性能が求められる用途に限られる。
NIMSによる磁気冷凍技術の開発
液化して水素を運搬するためには冷却技術の効率化が不可欠であり、研究が進められている。例えば、物質・材料研究機構は金沢大学などと協力して、磁気を用いた新たな冷凍技術を開発中だ※10。
水素吸蔵合金によるアプローチ
水素原子は金属の結晶構造内部に容易に侵入し、金属を脆くするという性質を持つが、この性質を利用した水素貯蔵方法も検討されている。
水素吸蔵合金は、水素と化学結合を形成、または、その結晶構造中に水素を取り込むことで水素を貯蔵できる。圧力を操作することで水素の出し入れが可能だ。
水素は吸蔵合金中で結晶構造に従って配列されるため、気体状態と比較して極めて高い水素充填率を実現できる。中には、体積にして液体水素の1/2、気体水素の1/1600にまで圧縮して水素を吸蔵できる合金も存在する※11。
圧縮水素と比較しても保存のためにそれほど大きな圧力が必要なく(10bar程度)、水素の出し入れが緩やかに進行するため、安全性が高いこともメリットだ。
実用化に向けた課題は重量と材料の希少性だ。車載などの用途を目指す場合、現状の重量ではエネルギー効率を大きく損なうため燃費が悪く、希少金属を利用するため車自体も高額になる。
これら課題を解決するために、合金以外の水素吸蔵物質も検討されてきた。水素吸蔵に求められる物性は水素を結晶構造内に取り込めるスペースを持つこと、なおかつ、繰り返しの水素の出し入れで自身が破壊されないことだ。
金属有機構造体(MOF)の応用
これら性質を満足する吸蔵物質としては、多孔質カーボンや金属有機構造体(MOF)が挙げられる。多孔質カーボンはリチウムイオン電池の電極に用いられるなど、製造と利用に関して多くの蓄積がある。MOFについては過去当サイトでも取り扱ったので、そちらも併せて参照して頂きたい。
参考記事:金属有機構造体(MOF)の技術開発動向
水素吸蔵合金スタートアップ
固体への水素吸蔵技術は未だ研究段階だが、海外ではいくつかのスタートアップが商用ストレージを販売している。
GRZ technologiesはスイス連邦工科大学のスピンオフとして2017年に設立された※12。
水素吸蔵合金を用いたDASH Storage Modulesは、寸法1200mm×928mm×1292mm、重量1.6tの水素ストレージで、屋外に据え置き利用する。研究機関などを主なターゲットとしているようだ。
一方、カナダのスタートアップであるH2Heatは、大規模、超長期の水素貯蔵を可能とするストレージを目指す※13。高温によって吸蔵合金と水素を化学的に結合させ、水素を安定に存在させることで、エネルギー損失を最低限に抑えることが可能だ。こちらは大規模な水素生産プラントと協業を目指しているように見える。
液体吸蔵の水素運搬技術を開発するHSL Technologies
変わったソリューションとしては液体に吸蔵させる、つまり、水素を液体に溶解させて運搬するという方法もある。フランスのスタートアップであるHSL technologiesは、非爆発性で無毒な水素化ケイ素誘導体に水素を溶解させて運搬する技術を開発した※14。同社は2023年にシリーズA資金調達ラウンドで13m€を調達している※15。
化学変化によるアプローチ
水素はそのままでは大きな空間を占有する上に液化が難しく扱いづらい物質だが、複素環式化合物やアンモニアなどに変換することで輸送が容易になる。
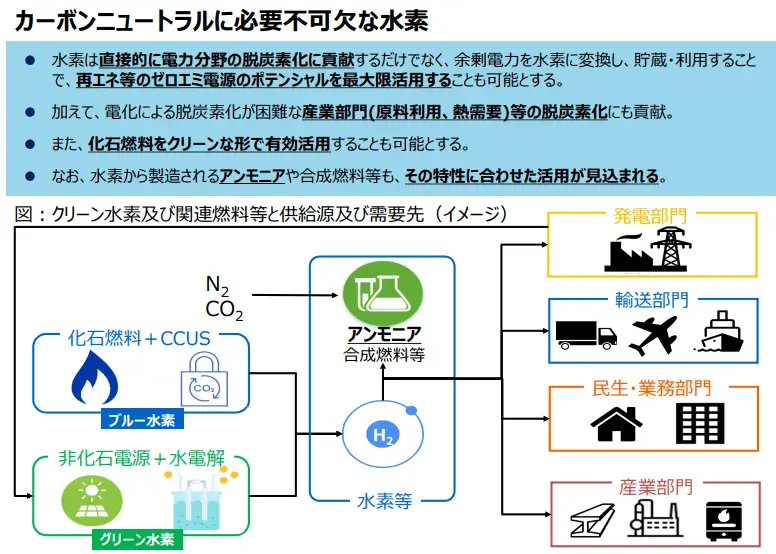
(令和4年4月19日資源エネルギー庁 省エネルギー・新エネルギー部 資源・燃料部)
このように別の物質に変換して水素を貯蔵・運搬する方式では、可逆性や変換コストが問題となる。トルエン、メチルシクロヘキサンなどは触媒存在下で加熱することで容易に化学反応が起き、逆の反応も可能だ。こうした可逆的な水素の出し入れが可能なキャリアを有機ハイドライドと呼ぶ。
一方、アンモニアを水素から製造する方法として有名なハーバー・ボッシュ法は高温・高圧が必要だ。逆反応としてアンモニアから水素を取り出すことも容易ではないため、実用的な意味で可逆性はない。アンモニアにする場合には、水素に戻すことを前提としない活用も検討されている。
日本の重工業企業であるIHIはCO2を排出しないアンモニア燃焼ガスタービンの開発に取り組む※16。
アンモニアは水素と同様、燃焼時にCO2を排出しない。ただし、CO2以上の温室効果を持つ窒素酸化物を排出することには注意が必要だ。IHIのガスタービンでは窒素酸化物の排出も抑えることに成功し、実用化へ大きく近づいた。
まとめ
ここまで見てきたように、水素市場が注目を浴びるとともに、水素貯蔵・輸送の方法についても、世界中の大手企業、スタートアップ、大学研究機関が活発に技術開発を推進している。
海外スタートアップの中には巨額の資金調達に成功する企業も出てきており、水素関連市場での競争が始まっている状況である。
参考文献:
※1 Navigating the Hydrogen Startup Ecosystem | Net Zero Insight(リンクはこちら)
※2 三菱重工、米で世界最大級の再エネ水素製造、岩塩空洞に貯蔵 | 日経BP(リンクはこちら)
※3 高圧水素輸送用ラインパイプ材の研究開発について ~石油メジャーが参画する日本財団とDeepStarの連携技術開発助成プログラムに採択~ | JFEスチール(リンクはこちら)
※4 NPROXX(リンクはこちら)
※5 1bar = 10^5 Pa ≒ 1気圧
※6 CUMMINS TO FORM JOINT VENTURE WITH NPROXX FOR HYDROGEN STORAGE | Cummins(リンクはこちら)
※7 搭載量5倍・コスト10分の1、トヨタが水素社会へ実証する「貯蔵モジュール」の全容 | ニュースイッチ(リンクはこちら)
※8 「水素で世界を動かせ」、トヨタの液体水素カローラが富士24時間レースを完走 世界初の挑戦は成功 | Car Watch(リンクはこちら)
※9 「水素液化貯蔵システムの開発」 Journal of Japan Society of Energy and Resources, Vol. 37, No. 4 (リンクはこちら)
※10「革新的水素液化技術への挑戦 ~実用的な磁気冷凍法による水素液化コスト削減に道~」 | 国立研究開発法人物質・材料研究機構 (リンクはこちら)
※11「水素吸蔵合金」 表面化学 Vol. 56, No. 4, 2005 (リンクはこちら)
※12 GRZ technologies(リンクはこちら)
※13 H2Heat(リンクはこちら)
※14 HSL technologies(リンクはこちら)
※15 Hydrogen startup HySiLabs raised €13 million | tech eu (リンクはこちら)
※16 世界初,液体アンモニア100%燃焼によるガスタービンで,CO₂フリー発電を達成 ~燃焼時に発生する温室効果ガスを99%以上削減~ | IHI (リンクはこちら)
【世界の水素の技術動向調査やコンサルティングに興味がある方】
世界の水素の技術動向調査や、ロングリスト調査、大学研究機関も含めた先進的な技術の研究動向ベンチマーク、市場調査、参入戦略立案などに興味がある方はこちら。
先端技術調査・コンサルティングサービスの詳細はこちら
CONTACT
お問い合わせ・ご相談はこちら

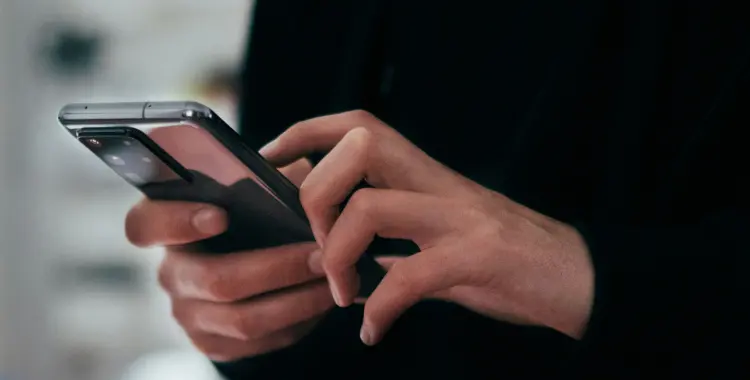